在新能源汽车行业的迅猛发展背景下,电池制造技术持续革新,特别是对电池极片表面清洗技术的要求愈发严格。利元亨的极片激光飞行清洗技术,以其无接触、无污染、高精度、低损伤的独特优势,正逐步确立其在电池制造领域的关键地位。作为21世纪最具发展潜力的绿色清洗技术之一,极片激光清洗技术在电池极片处理方面展示了广阔的应用前景,现已广泛融入极片制造、电芯制造及电池组装等核心的动力电池生产环节中。
面对传统静态清洗技术,成本高,效率低,不易维护等痛点,利元亨前瞻性地布局了极片激光飞行清洗工艺,通过自主研发的高效极片激光飞行清洗技术,成功解决了极片激光清洗过程中工艺兼容性差、清洗效率低、扫描路径复杂等难题,为优化新一代电池产品提供了全新的解决方案。
极片激光飞行清洗技术的核心优势在于其高效性、稳定性和激光利用率。在清洗过程中,激光束能够在材料表面连续移动,定位与出光同步进行,彻底消除了传统静态清洗方案中非有效加工时间的问题。这不仅大幅提高了清洗效率,还确保了清洗过程的高度一致性和可靠性。
然而,随着新材料和新工艺的不断引入,如何进一步提升激光清洗的质量和效率,特别是在飞行状态下实现激光扫描与轴联动,成为了一个亟待解决的挑战。利元亨在这方面进行了深入研究,持续攻克关键技术难题。通过优化运动控制系统,利元亨不仅提高了激光扫描与轴联动的精准度和稳定性,还确保了清洗质量,同时显著提升了清洗效率。
掌握核心科技:打造高效能激光清洗系统
1
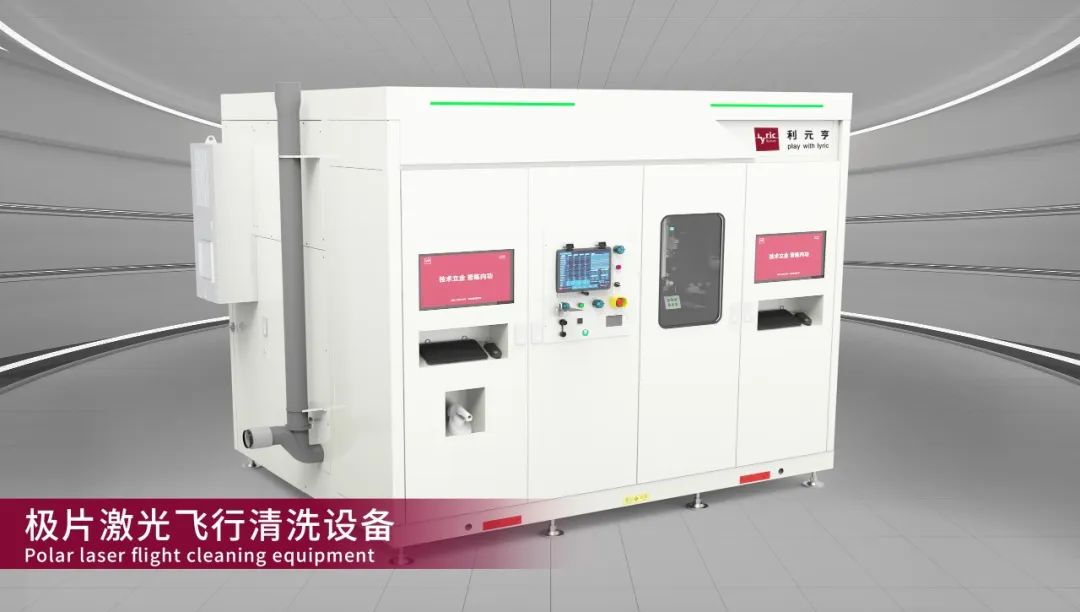
利元亨通过融合多项先进技术,不仅攻克了单一材料的清洗难题,还成功开发出适用于多种材料的高效极片激光飞行清洗技术。该技术系统由激光光学系统、PLC控制系统及飞行清洗工装三大模块组成,实现了电池极片全方位高稳定性的连续自动化激光清洗。设备性能卓越,能确保无残留、无针孔透光、外观无破损、无褶皱、无多清洗或漏清洗现象,检出率100%,单槽位清洗时间从0.8s降低到0.6s,并且走带速度达到或超过12米/分钟。这项技术极大地拓宽了激光清洗技术的应用范围,有效满足了客户在生产工艺、制造品质与成本控制方面的综合需求。目前,利元亨已实现对电池各规格极片的全自动化飞行清洗,确保清洗后的产品完全符合高标准的工业应用要求。
激光器研发:激光器和光路传输系统的优化,确保了激光光束质量和能量的稳定输出,通用控制接口支持广泛的频率范围,并提供多种脉宽选择,且支持在线修改,首脉冲可用,经过整形后的光斑及高光束质量保证了生产产品的高质量和高效率,风冷设计高效、方便、快捷安装与设计,降低了维护成本。
振镜扫描系统:通过优化激光光路系统的稳定性,确保了系统运行的稳定性和可靠性,实现最宽的视场和更长的焦距,通过20位SL2-100协议或16位XY2-100协议控制,数字PWM输出级极大地降低了功耗和热量,快速动态响应和高速度促进了生产效率,动态性能出色,速度快,功能全面。
飞行清洗工装:特有的紧固方式和优化设计,确保了清洗过程中的材料稳定性和无损伤,旋转清洗工装设计解决了复杂形状部件的清洗难题,显著提升了清洗效率,可选冷却方式包括水冷、油冷或风冷,保证了产品品质,结构布局合理,大大减小设备整体占地空间,可拆装结构方便更换,高效快速清洁维护与保养。
激光控制系统:自主研发的激光飞行清洗轨迹控制算法,确保了深度清洗的一致性,清洗过程的实时监控和动态调整方法,保证了清洗效果的稳定性和一致性,plc控制与激光控制系统协同工作,保证设备精度,自主研发软控算法,自定义清洗槽位与精准控制追踪轨迹。
高效除尘方案:确保极致洁净与安全
2
利元亨高效的除尘方案采用了抽风换气的工作原理,以清除空气中的游离粉尘。该方案配备了一个可调节的除尘系统,允许用户根据现场的具体环境条件自由调整风速大小与位置角度,从而实现最佳的除尘效果。通过运用流体分析工具进行关键因子的DOE设计,有效解决了生产过程中遇到的碎屑、残渣等问题。经验证,此除尘方案在清洁后可使表面洁净度达到99.9%以上,大幅提升了作业的安全性。

面对行业变化,利元亨展现出卓越的适应性和创新能力,准确把握新材料应用推动设备更新换代的关键时机。依托深厚的研发能力和对市场需求的敏锐洞察,在创新飞行清洗技术领域取得了决定性的进展,不仅大幅提升了客户的生产线效率,还增强了其成本竞争优势。
未来,利元亨将持续引领激光技术与锂电智能装备的发展潮流。通过加大研发投入,扩大市场覆盖范围,公司将进一步积累经验和技术,致力于创造更多具有行业影响力的前沿技术和工艺,为客户提供更加高效、更具价值的解决方案。
Lyric Pole Piece Laser Flight Cleaning: Precise Control, High Efficiency, Non-destructive
Amid the rapid development of the new energy vehicle industry, battery manufacturing technology continues to evolve, with increasingly stringent requirements for battery pole piece surface cleaning. Lyric''s Pole Piece Laser Flight Cleaning technology, with its unique advantages of non-contact, pollution-free, high precision, and low damage, is gradually establishing itself as a crucial component in battery manufacturing. As one of the most promising green cleaning technologies of the 21st century, pole piece laser cleaning technology demonstrates vast application potential in battery pole piece processing and is now extensively integrated into key stages of power battery production, including pole piece manufacturing, cell production, and battery assembly.
In response to the challenges of traditional static cleaning technologies, such as high costs, low efficiency, and difficult maintenance, Lyric has strategically developed the Pole Piece Laser Flight Cleaning process. Through its independently developed high-efficiency Pole Piece Laser Flight Cleaning technology, Lyric has successfully addressed issues like poor process compatibility, low cleaning efficiency, and complex scanning paths encountered in laser cleaning of pole pieces. This innovation provides a new solution for optimizing next-generation battery products.
The core advantages of Pole Piece Laser Flight Cleaning technology lie in its efficiency, stability, and laser utilization. During the cleaning process, the laser beam can move continuously across the material''s surface, with positioning and laser output occurring simultaneously, effectively eliminating the non-productive processing time found in traditional static cleaning methods. This not only significantly boosts cleaning efficiency but also ensures a high degree of consistency and reliability throughout the cleaning process.
However, with the continuous introduction of new materials and processes, enhancing the quality and efficiency of laser cleaning, particularly achieving laser scanning synchronized with axis motion in a flight state, has become an urgent challenge. Lyric has conducted in-depth research in this area, continually overcoming key technical difficulties. By optimizing the motion control system, Lyric has not only improved the precision and stability of laser scanning synchronized with axis movement but also ensured cleaning quality while significantly boosting cleaning efficiency.
1.Mastering Core Technology: Building a High-Performance Laser Cleaning System
By integrating multiple advanced technologies, Lyric has not only overcome the challenges of cleaning single materials but has also successfully developed a high-efficiency Pole Piece Laser Flight Cleaning technology suitable for various materials. This system comprises three main modules: the laser optical system, the PLC control system, and the flight cleaning fixture. It enables comprehensive, high-stability, continuous, and automated laser cleaning of battery pole pieces. The equipment boasts exceptional performance, ensuring no residue, pinhole transmission, damage, wrinkles, or over-cleaning/under-cleaning issues, with a 100% detection rate. The single-slot cleaning time has been reduced from 0.8 seconds to 0.6 seconds, and the web speed reaches or exceeds 12 meters per minute. This technology significantly broadens the application scope of laser cleaning, effectively meeting customers'' comprehensive needs in production processes, manufacturing quality, and cost control. Currently, Lyric has achieved fully automated flight cleaning of pole pieces for various battery specifications, ensuring that the cleaned products fully meet high industrial standards.
Laser Research and Development: The optimization of the laser and optical transmission system ensures stable output of laser beam quality and energy. The universal control interface supports a wide frequency range and offers various pulse width options, with online modification capabilities. The first pulse is readily available, and the shaped laser spot, along with high beam quality, guarantees high quality and efficiency of the produced products. The air-cooling design is efficient, convenient, and quick to install, reducing maintenance costs.
Galvanometer Scanning System: By optimizing the stability of the laser optical system, the stability and reliability of the entire system are ensured. It achieves the widest field of view and longer focal lengths. Controlled by the 20-bit SL2-100 protocol or the 16-bit XY2-100 protocol, the digital PWM output stage significantly reduces power consumption and heat generation. The system''s fast dynamic response and high speed enhance production efficiency, with outstanding dynamic performance, fast speeds, and comprehensive functionality.
Flight Cleaning Fixture: The unique fastening method and optimized design ensure material stability and damage-free cleaning during the process. The rotating cleaning fixture design addresses the cleaning challenges of complex-shaped components, significantly improving cleaning efficiency. Optional cooling methods, including water cooling, oil cooling, or air cooling, ensure product quality. The structure is reasonably laid out, greatly reducing the overall footprint of the equipment. The detachable design allows for easy replacement and efficient, quick cleaning, maintenance, and upkeep.
Laser Control System: The self-developed laser flight cleaning trajectory control algorithm ensures the consistency of deep cleaning. Real-time monitoring and dynamic adjustment methods during the cleaning process guarantee the stability and uniformity of the cleaning effect. The PLC control system works in tandem with the laser control system to ensure equipment precision. The proprietary soft control algorithm allows for customized cleaning slots and precise control of tracking trajectories.
2.Efficient Dust Removal Solution: Ensuring Ultimate Cleanliness and Safety
Lyric''s efficient dust removal solution adopts a ventilation and exhaust principle to eliminate free-floating dust particles in the air. The solution is equipped with an adjustable dust removal system, allowing users to freely adjust the airflow speed and angle based on the specific environmental conditions on-site, ensuring optimal dust removal performance. By utilizing fluid analysis tools for the DOE (Design of Experiments) of key factors, the solution effectively addresses issues such as debris and residue encountered during production. Verified results show that this dust removal solution can achieve a surface cleanliness level of over 99.9% after cleaning, significantly enhancing operational safety.
In the face of industry changes, Lyric has demonstrated exceptional adaptability and innovation, accurately seizing the key opportunities driven by the application of new materials to upgrade equipment. Leveraging its strong R D capabilities and keen market insights, the company has made decisive progress in the field of innovative flight cleaning technology. This has not only significantly improved customers'' production line efficiency but also strengthened their cost competitiveness.
In the future, Lyric will continue to lead the development trend of laser technology and intelligent equipment for lithium batteries. By increasing investment in R D and expanding market coverage, the company will further accumulate experience and technology, aiming to create more cutting-edge technologies and processes with industry impact, and provide customers with more efficient and valuable solutions.