将三个回收车间的平均净煤气含苯量从3g/Nm3降至1.16g/Nm3;2022年多回收粗苯990.8吨,创造经济效益574.7万元;多次在技术创新方面作出突出贡献;被山西焦煤授予首个“三年三步走”三级功勋团队荣誉称号……
一份份亮眼的成绩单,证明了这支团队在创新突破中的竞争实力,他们就是山西焦化化产品回收厂“降低净煤气含苯‘精益创新管理’”项目团队。
齐心协力开良方
近年来,化产品回收厂狠抓精益化管理和技术创新工作,成立了“降低净煤气含苯‘精益创新管理’”项目团队,深入开展降低煤气含苯技术攻关,以提质增效和减少浪费。该团队致力于技术研究和攻关。起初,通过不断优化循环洗油量和蒸汽量工艺指标、进一步改善洗油质量等一系列措施,将净煤气含苯量由3g/Nm3降至2g/Nm3,精益化管理取得了一定成效。
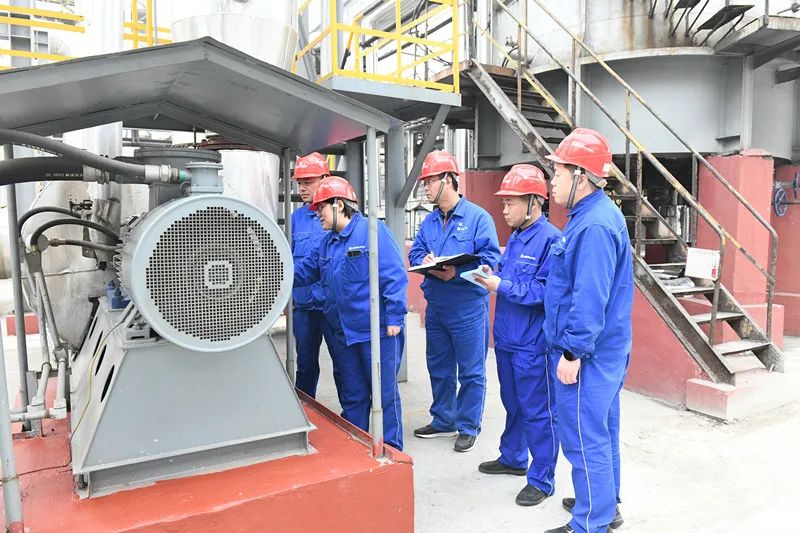
技术创新没有止境,随着生产模式的变化和持续改进,工艺参数也需要新的突破。根据公司精益化管理工作要求,为进一步提质增效、降低成本,团队里的每一位成员主动与厂领导签订承诺书,立下军令状,挑战一项项艰巨的任务。
为实施精益化生产,降低煤气中的含苯量,连续1个月,团队成员每天7点准时到岗,晚上9点下班,通过一次次调研、一次次数值模拟和实验,最终,将入脱苯塔富油温度调至≥120℃,管式炉后富油温度由170—180℃提高到175—185℃,脱苯塔底温度由170℃提高到175℃,贫油温度由32℃降低至30℃。
“这个团队从来没有让大家失望过,那段时间他们拧成一股绳,全身心投入到工作中,无惧劳苦、敢于拼搏,一点一点地试、一度一度地调,最终找到了最佳生产模式,这些数字的背后彰显着团队每一位成员过硬的技术。”化产品回收厂厂长赵文栋欣慰地说。
此外,他们还通过不断优化煤气洗脱苯工艺流程,强化换热器管理,减少了热量浪费。将粗苯管式炉前富油温度由120℃提高至135℃,稳定了脱苯塔温度,年可节约管式炉煤气消耗成本33.41 万元。
“集”中生智破难题
栗艳平是化产品回收厂生产科科长,也是“降低净煤气含苯‘精益创新管理’”项目团队的主要负责人之一。这些年,她带领团队成功攻克了一系列技术难题,打过几次漂亮仗,技术改造对于她来说并不陌生,召开项目专题会、编制方案等工作她都有着丰富的经验。
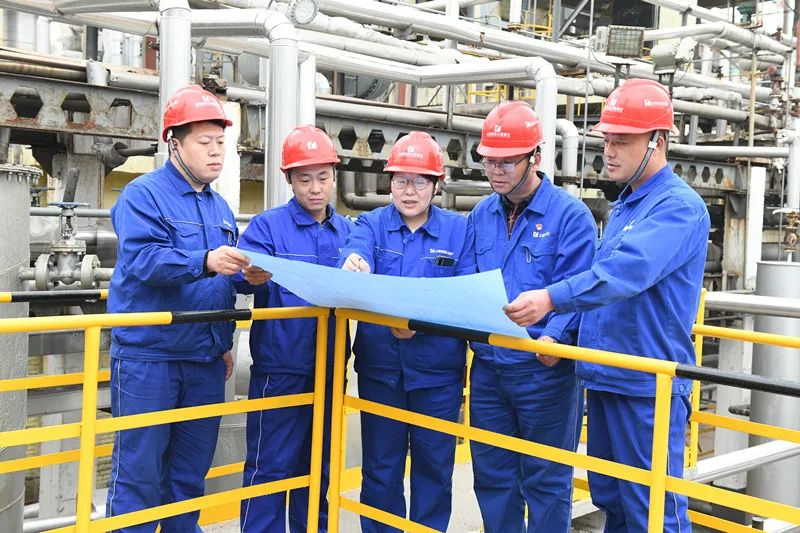
这一次的“三系统洗苯塔填料”升级改造项目对于栗艳平来说是一次艰巨考验。改造中三回收洗苯塔采用哪种填料、填料所需的数量以及类型等,都需要可靠的技术数据支撑。为了找到答案,栗艳平和团队成员四处搜集技术资料,大家一边自学一边请教,一次次拜访业内知名专家,一遍遍与同行业技术人员沟通交流。
技术资料是基础,编制项目施工方案是保证施工质量的第一步棋。在编制方案中,他们群策群力,先后编制完成了洗苯塔及粗苯装置检修开停车方案、洗苯塔检修工艺处置隔离方案、洗苯塔填料装填方案、洗苯塔花环填料检验方案、洗苯塔检修环保专项方案、洗苯塔检修安全专项方案等近30种方案和施工明细,为技术改造打好了坚实基础。
经过大家的努力,此次改造巧妙地将花环填料改造为不锈钢波孔板填料,改造后粗苯的吸收效果得到明显改善,系统阻力进一步降低,第三煤气回收车间的净煤气含苯量由1.97g/Nm3降至0.92g/Nm3,洗苯塔阻力由6KPa降至1KPa。
“每一项技术创新都是前所未有的挑战,我们就像过关斩将一样,不停地迎接各种难题。”该团队成员马晓强回忆,“虽然当时很辛苦,但是过后很有成就感。”
“线上”汇聚同发力
“感谢各位领导的指导和点评,大家刚才提出的建议,让我们茅塞顿开,我们将及时更正……今天的线上讨论会到此结束。”随着信息化时代的到来,该团队紧跟步伐,依托微信平台,过起了无“微”不至的“微”生活。
为了使各层面的相关人员及时掌握工艺指标参数,他们搭建了由厂领导、车间主任、技术骨干人员等相关人员组成的粗苯技术攻关微信攻关群,方便大家及时沟通解决生产问题。
起初,建立攻关群只是为了将每个时间段的生产情况和工艺参数及时发至群内,久而久之,方便快捷的优点得到干部员工的普遍认可。“针对技术攻关中遇到的困惑和需求,群内迅速响应。我们坚持线上及时回复、线下尽快解决原则,建立了完善问题办理机制,并就解决问题进展情况及时反馈。我们还定期挑选群内争议较大、交流频率较高的热门话题作为重点,安排专人进行专题授课,效果特别好。”团队队员李健介绍道,自从有了这个攻关群,工作效率提升了,大家的不少困难都得到了解决。
循环洗油长期运行后质量变差的问题,也是在这个攻关群里解决的。根据循环洗油质量调整再生器的排渣频次,由每周1次改为每周2次;根据运行情况及时对洗油槽底部沉积物进行清理,每季度对回收油库洗油槽液位排空一次;强化进厂原料管控,加强外购洗油取样分析监督,确保洗油质量。最终敲定的这三个硬举措不仅改善了洗油质量,还将循环洗油270℃前馏出量由50%提高至80%。