遵义海螺盘江水泥有限责任公司(下称“遵义海螺”)是一家专营水泥建材及光伏板生产的制造企业,近年来该企业通过余热发电、水体循环、除尘改造、垃圾滤液处理等有力措施,在节水节电降尘除污等方面均有建树,并通过优化工厂生产生活环境,打造“花园式”水泥工厂。2022年,坚实的绿色发展步伐让遵义海螺获评工信部授牌的国家级“绿色工厂”。
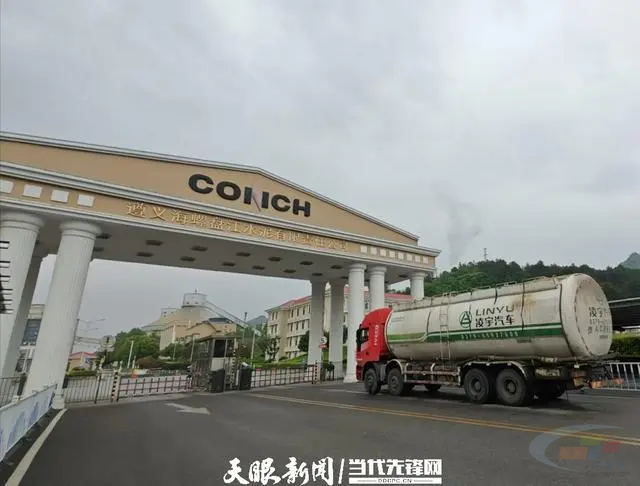
遵义海螺盘江水泥有限责任公司。
5月14日午间时分,走进位于遵义市汇川区的遵义海螺公司,公司设备保全处副处长林金华和同事午饭后在厂区的人工湖旁消食聊天。
眼前的湖水,是员工生活用水及水泥生产用水处理得来,靠近湖边不仅闻不到异味,湖畔茂密的植被反而引来阵阵花草香味。
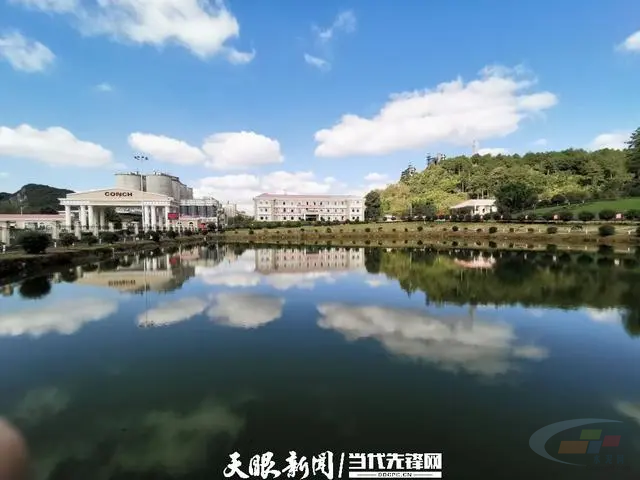
海螺水泥“一池三用”。(遵义海螺供图)
“这不仅是厂区景观湖,也是雨水收集池,同时也是生产用水中转池,可谓‘一池三用’。”林金华介绍,作为一家年产水泥熟料360万吨、水泥440万吨的大型水泥制品生产企业,集约节约用水一直是企业绿色生产的“风向标”。
水是水泥重要的生产要素,据贵州省水泥生产相关指标显示,每生产1吨水泥需约耗水0.6吨。
为节约生产生活用水,海螺水泥2012年投产之初便修建了人工湖,构建起厂区水体循环系统,水泥生产环节的中水通过在人工湖静置降温后,可通过管道返回至生产车间为设备冲洗降温,从而节省水耗。
水体循环的畅通给厂区带来了良好的生态。“人工湖岸边不仅种植了蔷薇、月季等植被,还有员工自种的辣椒、白菜等作物,沿岸灌木丛里时不时有野兔出没,湖里有2000多条鱼,要是你早来两个月,甚至能在人工湖岸边看到上百条鲤鱼产卵的情景呢。”林金华打趣道。
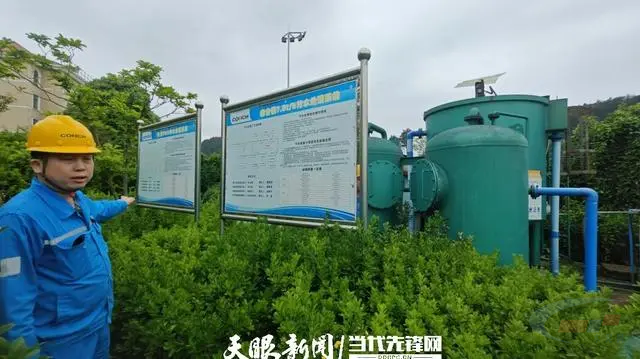
生活污水处理设备。
目前,遵义海螺已建成5套厂区污水处理设备,生活污水处理量达13.5立方米/小时,通过搭建水体循环系统,生产用水利用率超90%,水泥生产吨均水耗仅为0.17立方米,优于贵州省定额标准值的0.6立方米。
除了水体循环,遵义海螺还在节电道路上持续探索“黑科技”。
水泥生产的煅烧环节会产生上千摄氏度的高温,在窑尾会降至350℃左右,其间存在大量的废气余热可以利用。
海螺水泥为此配套了1×18兆瓦的余热发电系统,利用水泥熟料生产过程中废气余热进行热交换,生成水蒸气带动电机发电,每吨熟料发电量能达到40度以上,能解决水泥熟料生产77%的用电量,每年节约用电1.5亿度左右,节约电费约8000万元。
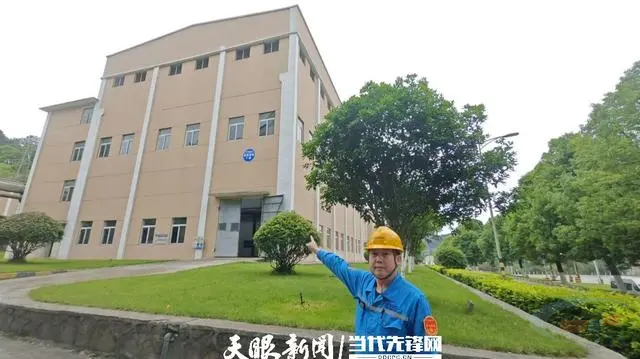
遵义海螺余热发电厂房。
“不仅如此,我们还利用窑尾余热供办公楼、食堂、宿舍暖气,给员工提供更加舒适的生活环境的同时,也减少空调用电,大幅降低生产及生活中的能源消耗,持续实现废气余热的高效循环利用。”站在厂区VG锅炉室前,林金华介绍。
节水省电双管齐下,海螺水泥在节能降碳领域开辟出新赛道。2020年,遵义海螺被工信部评为贵州省水泥行业唯一一家重点行业能效“领跑者”称号,近年来先后获得国家级“绿色矿山”“绿色工厂”、全国第三批“建材行业百家节能减排示范企业”、贵州省节能示范单位等十余项与节能降碳相关的国家级、省级荣誉称号。
不同于普通的水泥企业,行走在遵义海螺生产厂区,不仅闻不到烟尘、看不见煤灰,行走一路尽是花红柳绿的茂密植被。
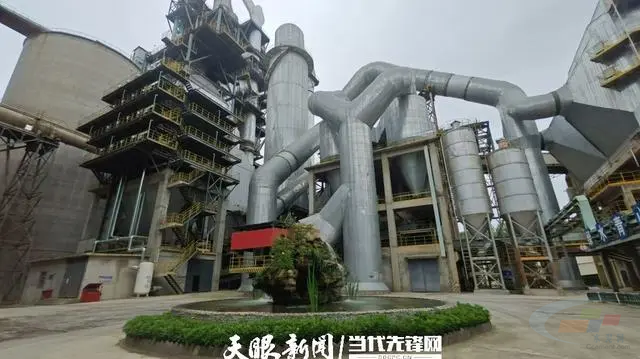
大气除尘系统。
清新的空气和靓丽的环境源自企业对大气改造“痛”下决心!
“生产水泥会伴生大量的粉尘、二氧化硫氮氧化物等有害气体,对大气环境和员工身心造成影响。为此,2018年至今我们累计投入超1.4亿元专门用于大气改造。”林金华说。
2018年,海螺水泥投资4000万元将水泥生产尾气电收尘工艺改为袋收尘,改造后厂区气体浓度为10mg/m3,远优于国家标准的50mg/m3。
次年,海螺水泥花费3000万元改良脱硫除尘工艺,通过湿法脱硫将二氧化硫含量控制在100mg/m3以内,优于国家标准的200mg/m3。
2022年,海螺水泥投资7000多万元建起了SCR烟气脱硝设备,将氮氧化物含量控制在100mg/m3以内。
严控的排放标准和低碳的生产能耗让海螺水泥能有序高效地进行生产。2023年,海螺水泥生产水泥熟料220万吨、水泥210万吨。今年1至4月,企业生产水泥熟料49万吨、水泥53万吨。
“下一步,我们将围绕节能减污降碳目标,用好“水循环”“热生电”“净大气”等生态妙招,持续挖掘新质生产力,对构建全省建材行业绿色低碳循环发展经济体系,以及贵州国家生态文明先行区的建设发挥示范引领作用。”遵义海螺公司总经理杨进说。